What do sustainable Fashion design and Tetris have to do with each other? For both, there is an interesting challenge in fitting together different forms in such a manner that the playing field is filled up.
To the fashion designers, the game has an environmental aspect. To develop garments, they usually spread a piece of material on a table and chop each piece to join them to create the clothing.
The problem that needs to be solved is the problem of reducing leftover material to the least possible amount (or zero waste fashion design), which harms the air, water, and soil.
As a step towards creating better sustainability in clothing, computer scientists from MIT’s CSAIL, the University of Washington and Adobe have created a software tool that aids designers in maximizing the use of their fabric.
The research was published by the ACM in the Proceedings of the 37th Annual Symposium on User Interface Software and Technology.
The computer application they have is called “WasteBanned” where you can design, edit, and even preview how your designs for pants, hoodies, and skirts will turn out.
After that, you can print the blueprint on a piece of paper in a manner that corresponds to the size of the garment and where the users have to cut their material to make their sustainable fashion designs a reality.
‘Zero waste design can be a really hard puzzle, but it’s rewarding to solve it,’ says former CSAIL postdoc, Adobe research scientist, and senior author Mackenize Leake.
Clothes appear to be very basic indeed, but the moment you alter one piece, you are also changing the others.
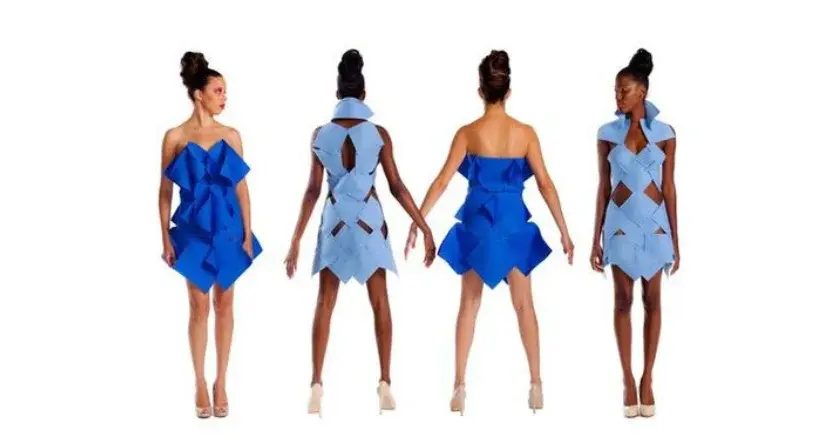
This is called linked editing and is a complex process that involves creativity, and WasteBanned is an entertaining way to see these changes before starting to trim.
It’s a shame that we don’t see more people design in this more environmentally friendly, resourceful way.
WasteBanned could be a move from the traditional concept of ‘designing clothes first’ to a more ‘material-first’ concept where the available material is given preference over what the piece of clothing is supposed to look like.
The tool then shows how each part, or panel, would look like as flat shapes before it demonstrates how the proposed apparel would look like in 3D.
The researchers’ computer-aided design tool allows users to input the dimensions of their fabric, and then design, cut, stitch, relocate, measure and label panels.
Users can then cut the panel into multiple edges, make a slit in the fabric or split an edge by making a break point.
For instance, you could draw a skirt from three pieces and name them as the front piece, back right piece, and back left piece then join them virtually.
You could also design a sweatshirt in 13 panels and number each panel and then sew as indicated on the panel.
The WasteBanned app also enables you to cut, undo or redo on any part that has been edited, which is a contrast to the real world where one cannot reverse the cutting of a design.
Users can also add constraints (or restrictions), for instance, zero waste limits that make you use all your material, and user-added restraints that limit the kind of cuts you make (for example, only vertical or parallel cuts).
When you are working on your 2D design, you will notice that the alterations you make will be represented as simple figures on a virtual model.
To make the design real, a user clicks the ‘simulate’ button to turn the garment into a real life 3D piece of clothing worn by the dummy.
A Simple Tool For Advanced And New Designers
The researchers also performed a user study with six participants, some of whom were experienced designers and some of whom had sewing experience.
Altogether, they noted that WasteBanned was convenient and fun to use. One user who had an undergraduate degree in fashion was able to take their digital designs and create a bell sleeve tunic from pink floral fabric that had been traced from the outline.
In their words, participants had various backgrounds, according to lead author and Flex software engineer Ruowang Zhang MEng.
Their consensus was that WasteBanned was very interesting and easy to use.” They also noted how it enhances sustainability – an aspect that goes against the design processes that you find in fast fashion.
Zhang and Leake pointed out that although their software tool is a good start toward “materials-first” design, they want to assist users in finding a set of seam curves with the same length as the other that would result in well-fitting and fashionable garments.
Also, the team is thinking about creating a specific constraint solver, allowing curved cuts and seams of different length.
‘Designing for material and ecological efficiency at the conceptual stage is the key to developing more sustainable forms of product manufacturing,’ explains Jennifer Jacobs, Assistant Professor at the University of California at Santa Barbara, who did not participate in the paper.
WasteBanned is interesting in this regard because the authors employ computational constraints to the material-first approach of the zero-waste clothing design that could reduce the thresholds for employing zero-waste methods in garment design in general.
“This work rethinks the process of apparel design in a neat way: The notion that you will use up all the fabric is inherent in the concept and the system does not allow you to design garments that cannot be made without waste, notes Steve Marschner, Professor of Computer Science at Cornell University not involved in the research.
‘This makes it easier, but much more difficult at the same time.’
You can’t draw one piece into a different shape without having to redraw the piece on the other side of the cut line and then also have to redraw other pieces that get attached to those, and it snowballs quickly.
WasteBanned addresses the constraints persistently, allowing the designer to freely experiment with what will be effective without having to consider all the ineffective options.
It is a big deal when reducing waste in the garment industry because a lot of fabric is consumed, and it is good to see that head-on tackling the connection between design and efficiency is being done.